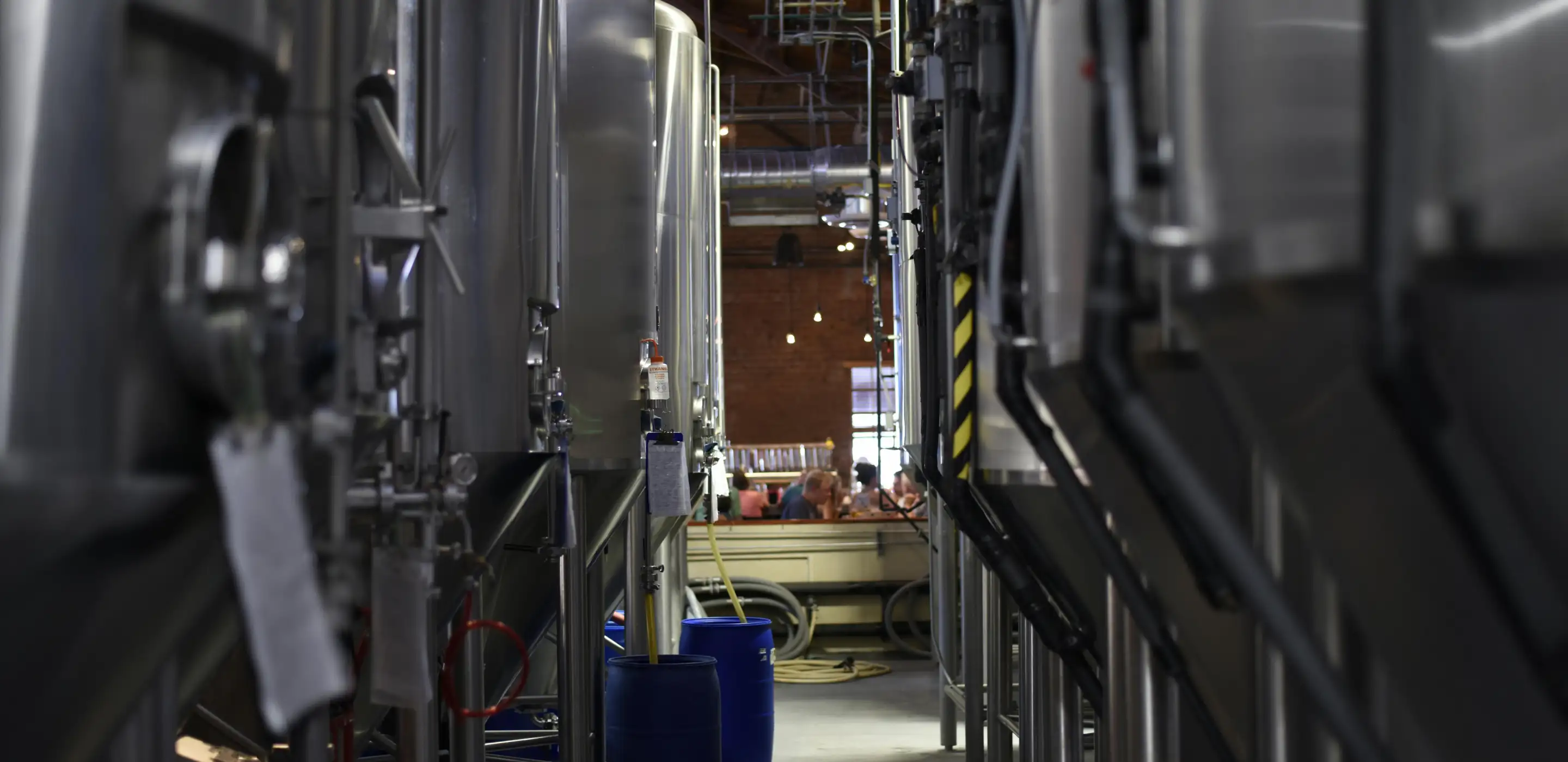
Hands on control and monitoring
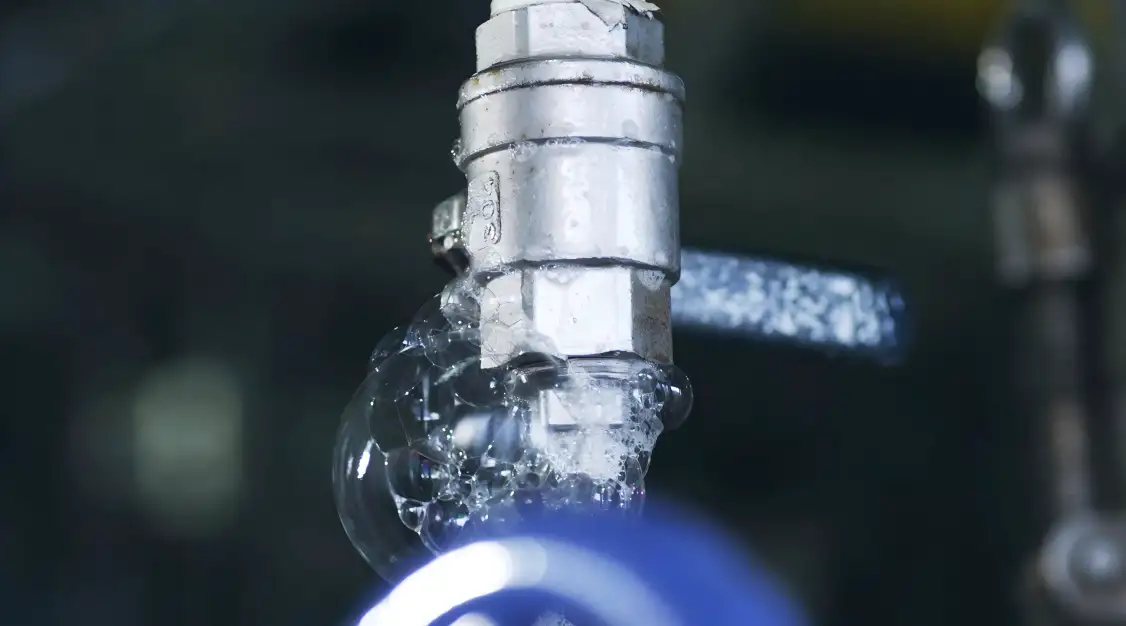
In the past, leak detection demanded substantial resources in terms of manpower, materials, and time, leading to high operational costs. For instance, using soapy water to identify leaks in a chemical plant could take several weeks. Furthermore, for safety reasons, leak detection was often limited to production shutdown periods, adding to the overall complexity and expense.
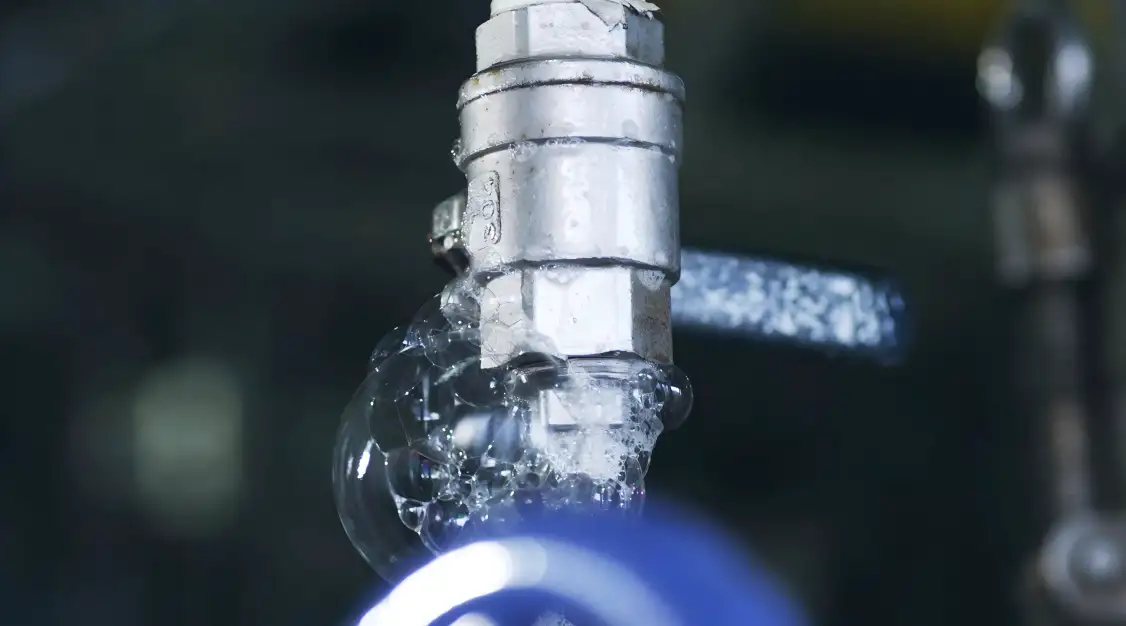

Unlike traditional leak detection methods like soapy water or gas concentration alarms, CRYSOUND utilizes advanced acoustic imaging technology to detect leaks. Our system identifies the distinct sound frequencies generated by gas leaks, enabling safe and efficient detection from a distance, regardless of the gas type.

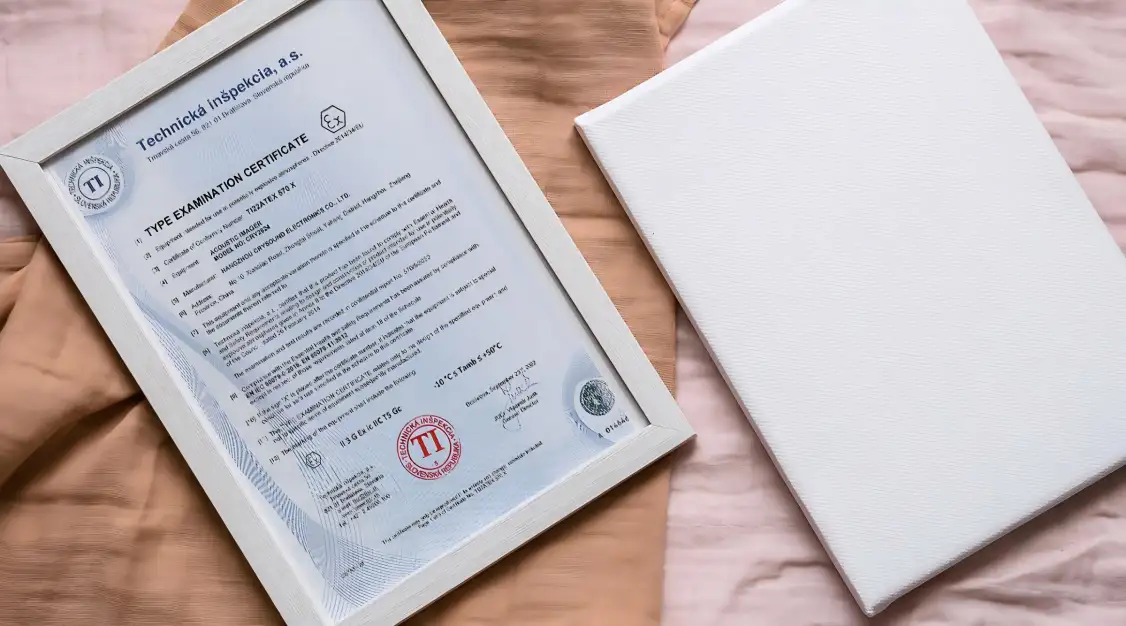
The ATEX-certified CRYSOUND acoustic imaging camera has demonstrated exceptional effectiveness in detecting hazardous gases like hydrogen and acetylene, ensuring the safety and reliability of equipment in the field.
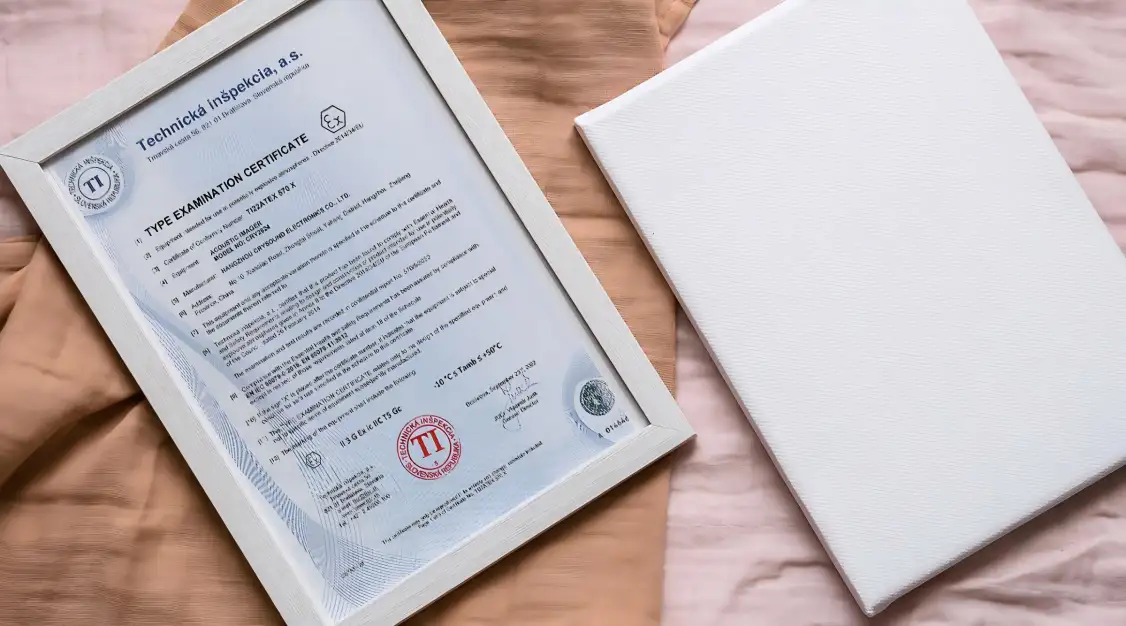
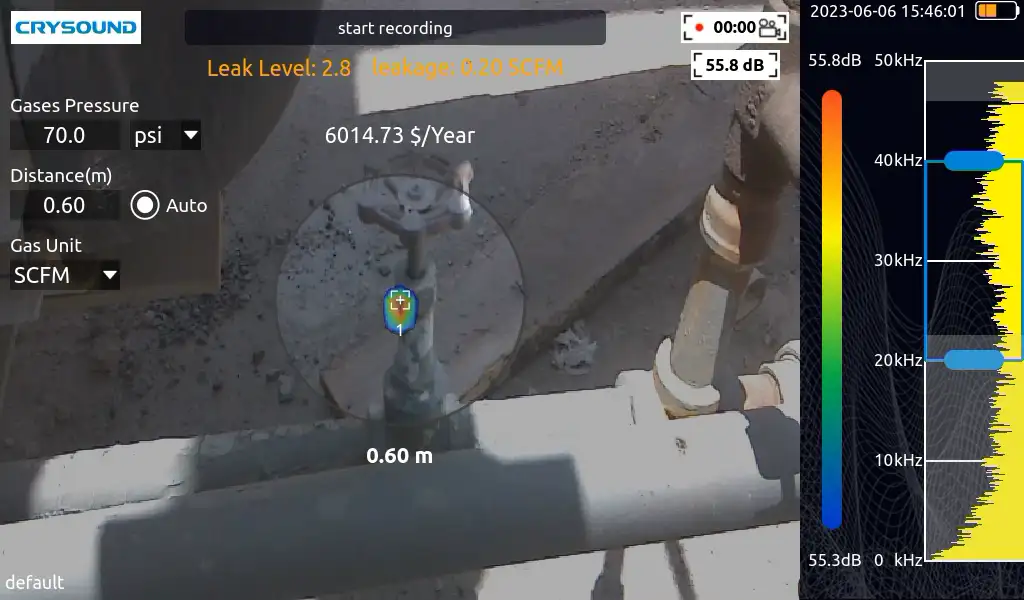
Chemical plants benefit greatly from acoustic imaging technology, which reduces the need for extensive materials, manpower, and time, ultimately driving down overall costs. This technology simplifies the detection of even small leaks of toxic or explosive gases, making it easier to align safety protocols with reliability objectives.
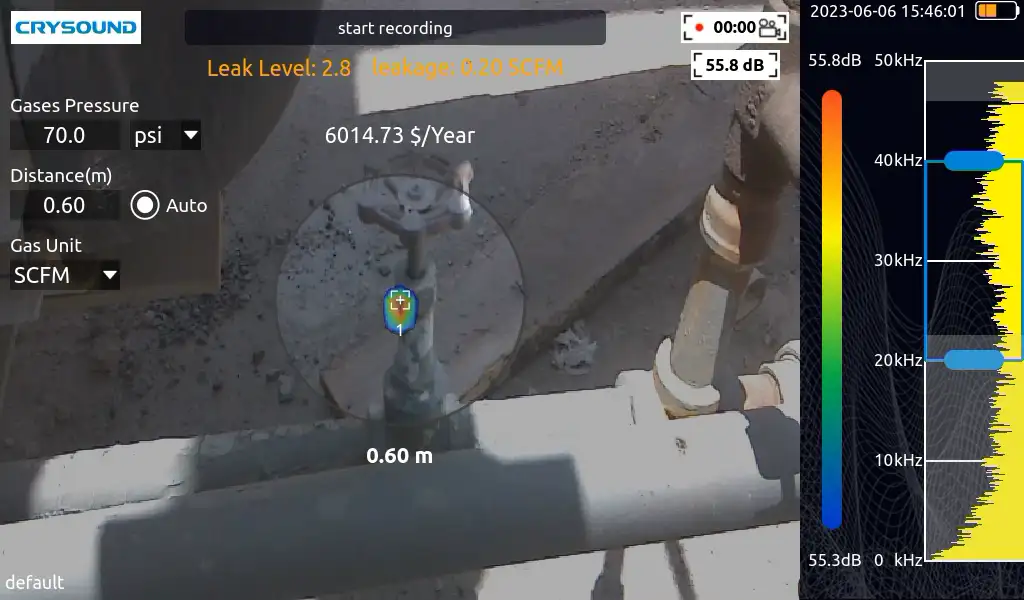
In the past, leak detection demanded substantial resources in terms of manpower, materials, and time, leading to high operational costs. For instance, using soapy water to identify leaks in a chemical plant could take several weeks. Furthermore, for safety reasons, leak detection was often limited to production shutdown periods, adding to the overall complexity and expense.
In the past, leak detection demanded substantial resources in terms of manpower, materials, and time, leading to high operational costs. For instance, using soapy water to identify leaks in a chemical plant could take several weeks. Furthermore, for safety reasons, leak detection was often limited to production shutdown periods, adding to the overall complexity and expense.
In the past, leak detection demanded substantial resources in terms of manpower, materials, and time, leading to high operational costs. For instance, using soapy water to identify leaks in a chemical plant could take several weeks. Furthermore, for safety reasons, leak detection was often limited to production shutdown periods, adding to the overall complexity and expense.
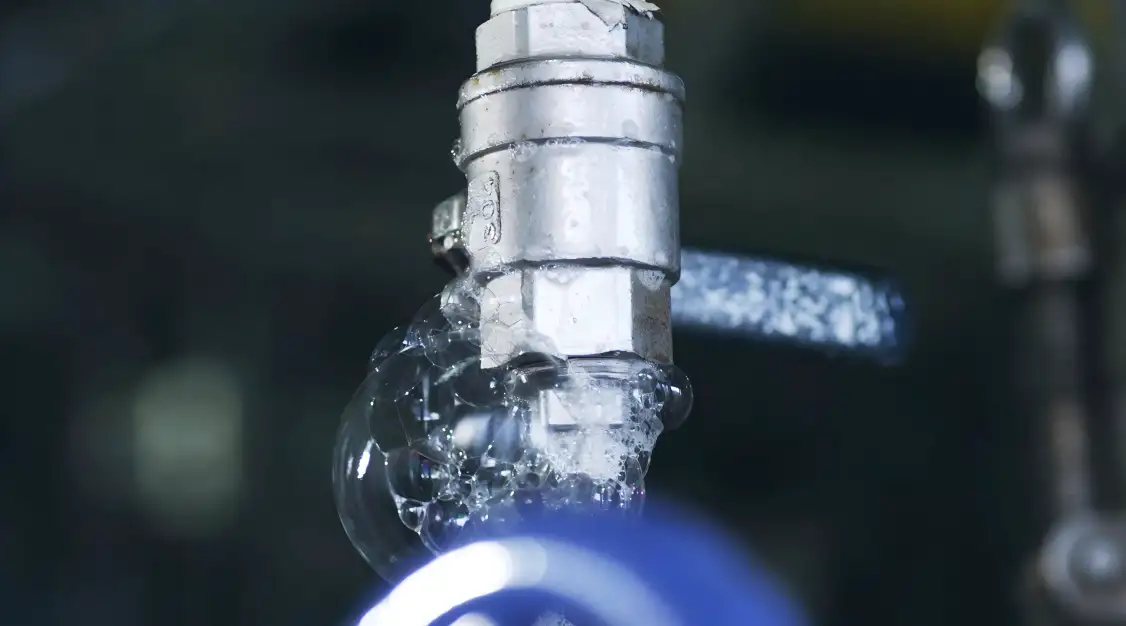
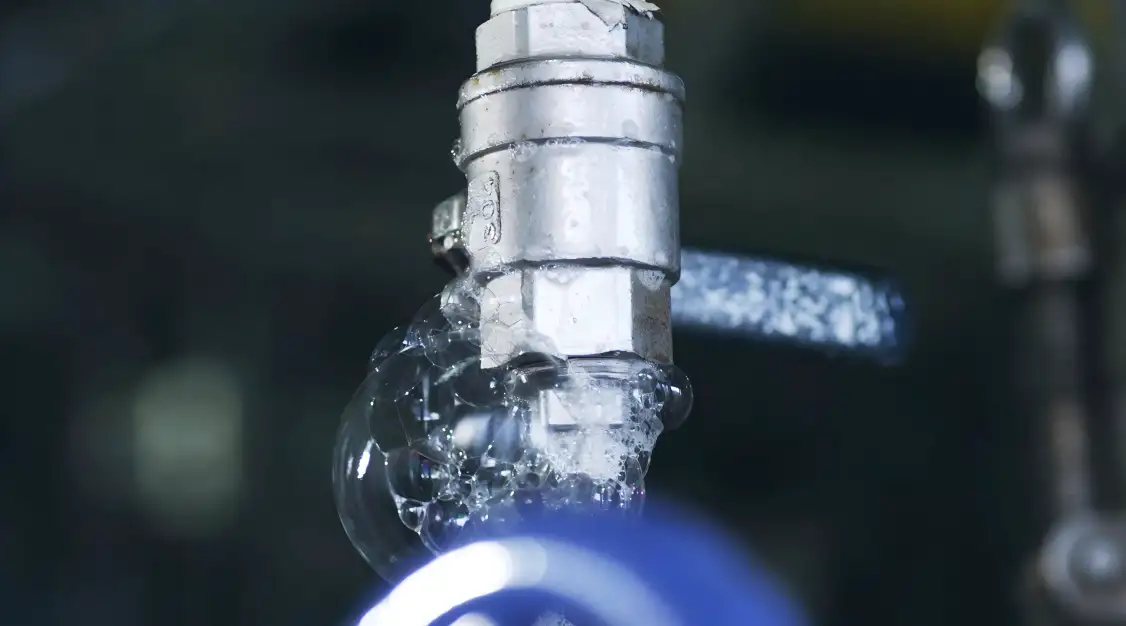
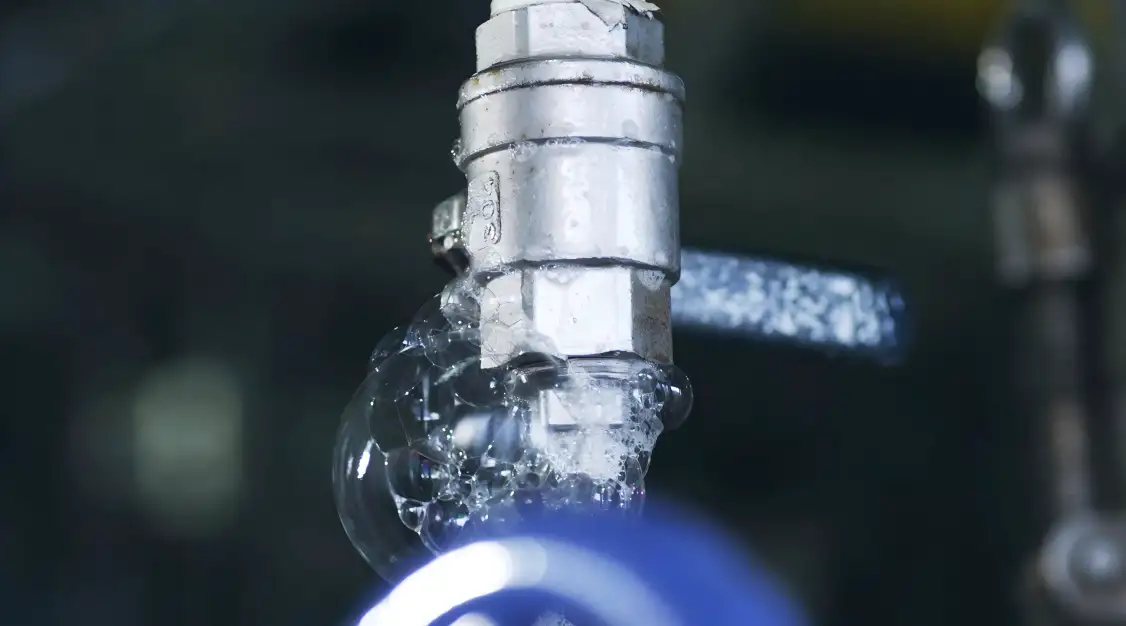
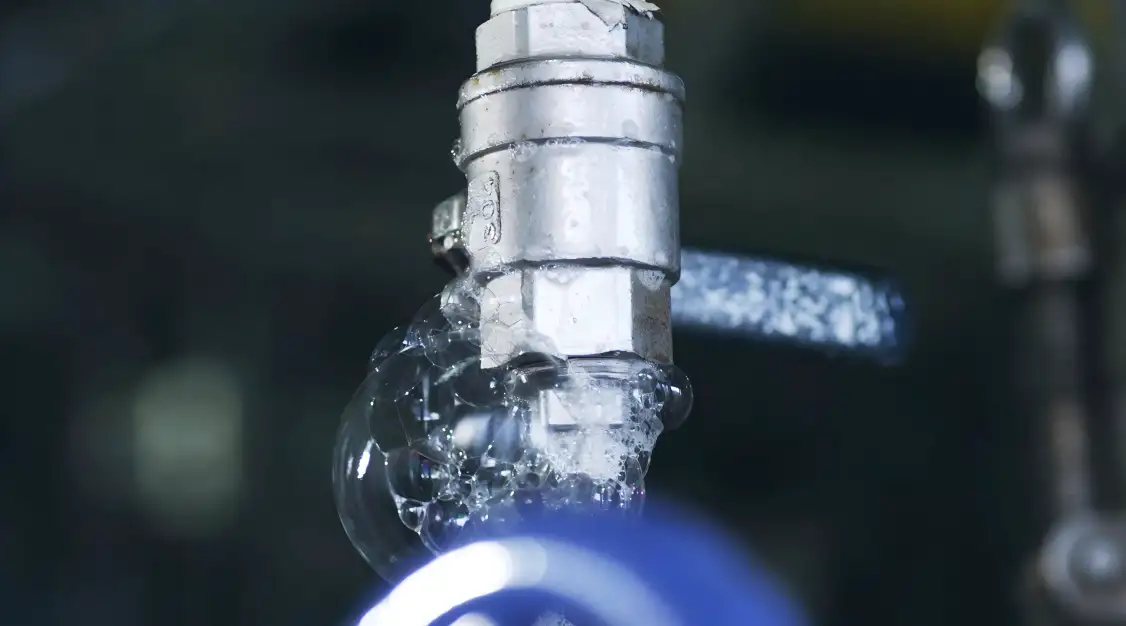
Unlike traditional leak detection methods like soapy water or gas concentration alarms, CRYSOUND utilizes advanced acoustic imaging technology to detect leaks. Our system identifies the distinct sound frequencies generated by gas leaks, enabling safe and efficient detection from a distance, regardless of the gas type.
Unlike traditional leak detection methods like soapy water or gas concentration alarms, CRYSOUND utilizes advanced acoustic imaging technology to detect leaks. Our system identifies the distinct sound frequencies generated by gas leaks, enabling safe and efficient detection from a distance, regardless of the gas type.
Unlike traditional leak detection methods like soapy water or gas concentration alarms, CRYSOUND utilizes advanced acoustic imaging technology to detect leaks. Our system identifies the distinct sound frequencies generated by gas leaks, enabling safe and efficient detection from a distance, regardless of the gas type.




The ATEX-certified CRYSOUND acoustic imaging camera has demonstrated exceptional effectiveness in detecting hazardous gases like hydrogen and acetylene, ensuring the safety and reliability of equipment in the field.
The ATEX-certified CRYSOUND acoustic imaging camera has demonstrated exceptional effectiveness in detecting hazardous gases like hydrogen and acetylene, ensuring the safety and reliability of equipment in the field.
The ATEX-certified CRYSOUND acoustic imaging camera has demonstrated exceptional effectiveness in detecting hazardous gases like hydrogen and acetylene, ensuring the safety and reliability of equipment in the field.
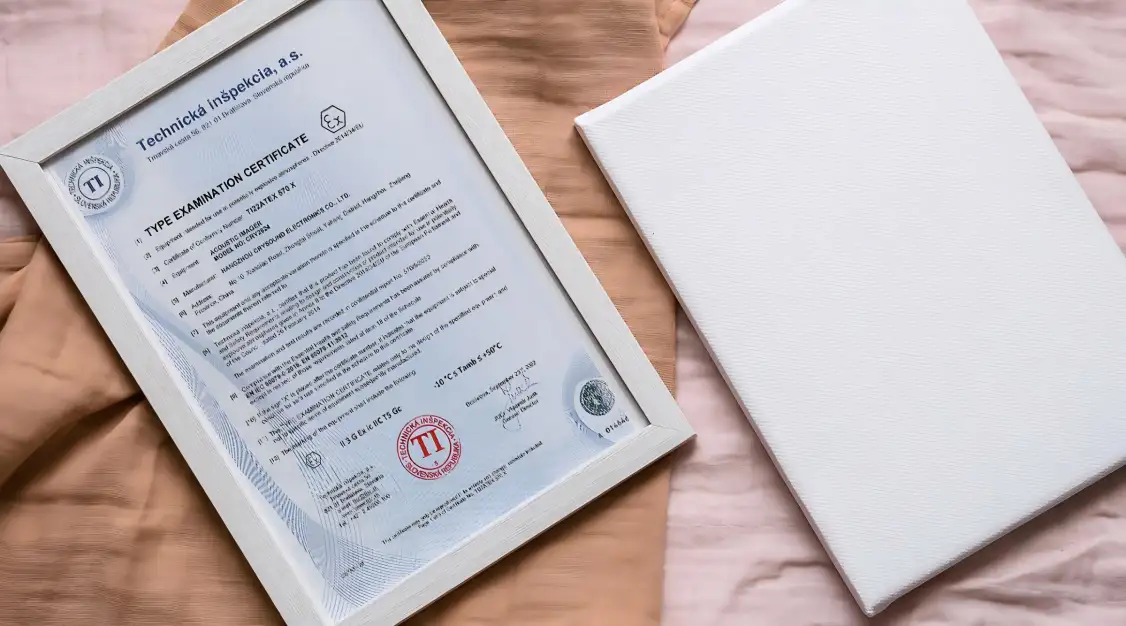
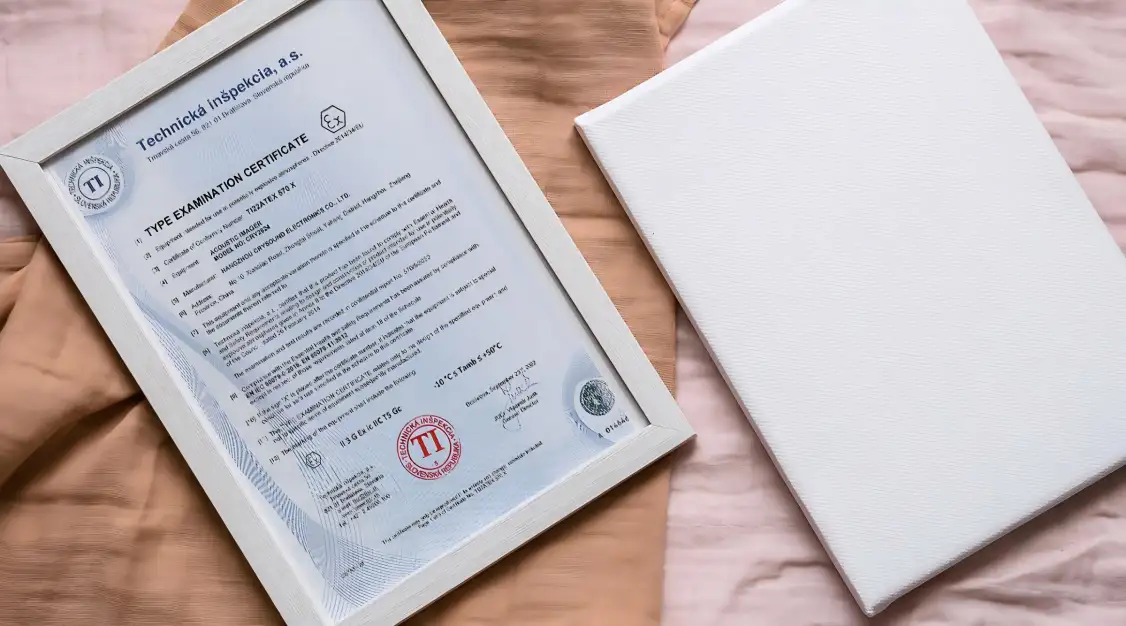
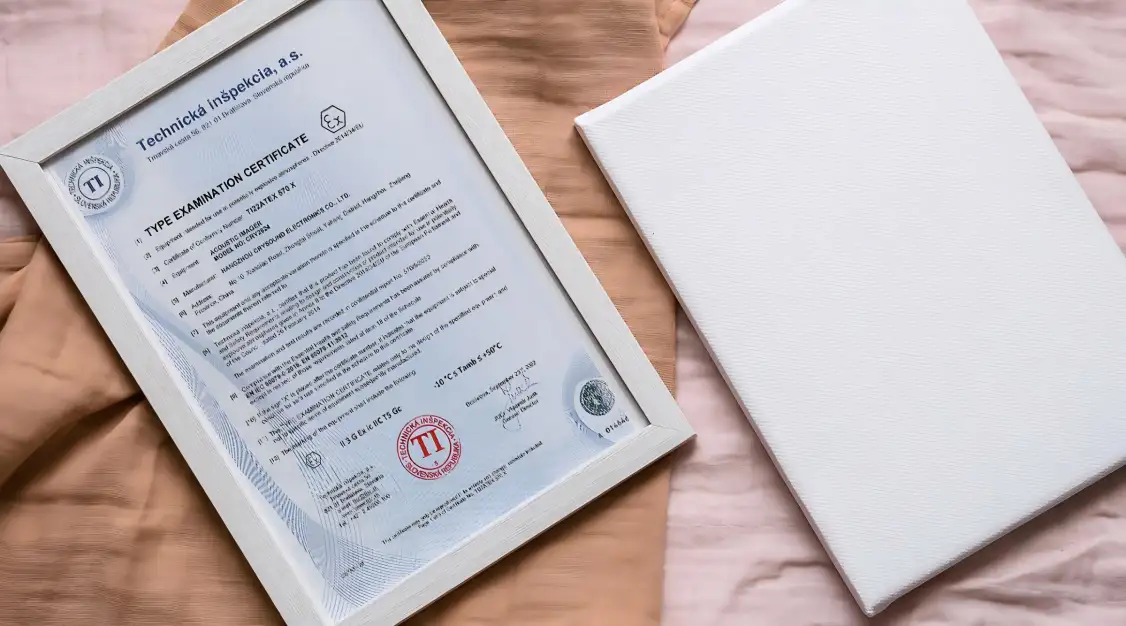
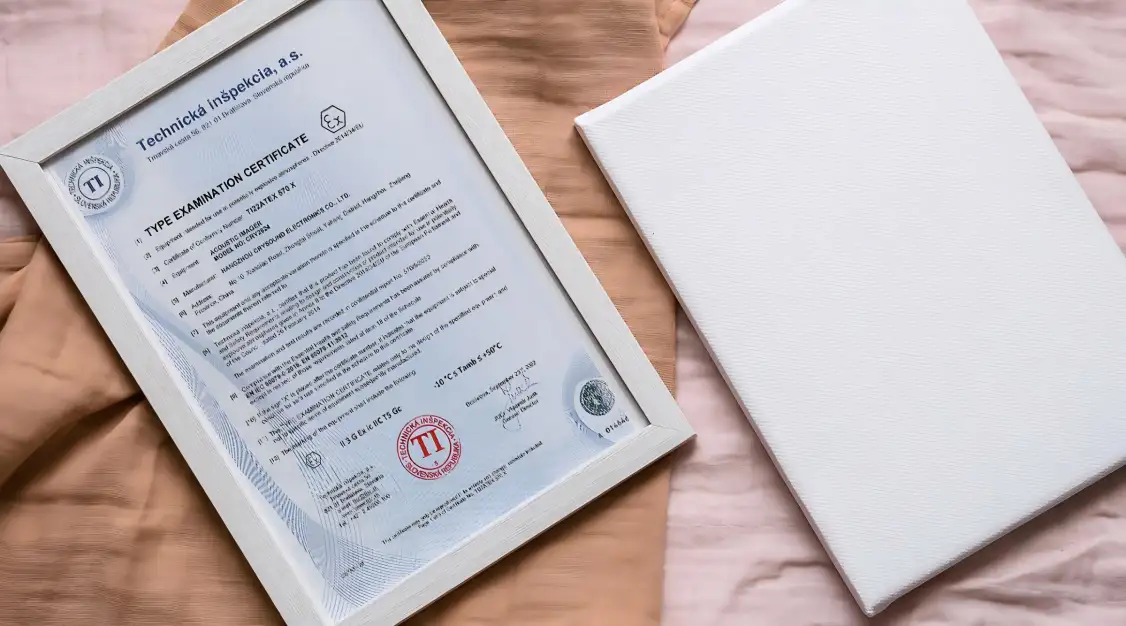
Chemical plants benefit greatly from acoustic imaging technology, which reduces the need for extensive materials, manpower, and time, ultimately driving down overall costs. This technology simplifies the detection of even small leaks of toxic or explosive gases, making it easier to align safety protocols with reliability objectives.
Chemical plants benefit greatly from acoustic imaging technology, which reduces the need for extensive materials, manpower, and time, ultimately driving down overall costs. This technology simplifies the detection of even small leaks of toxic or explosive gases, making it easier to align safety protocols with reliability objectives.
Chemical plants benefit greatly from acoustic imaging technology, which reduces the need for extensive materials, manpower, and time, ultimately driving down overall costs. This technology simplifies the detection of even small leaks of toxic or explosive gases, making it easier to align safety protocols with reliability objectives.
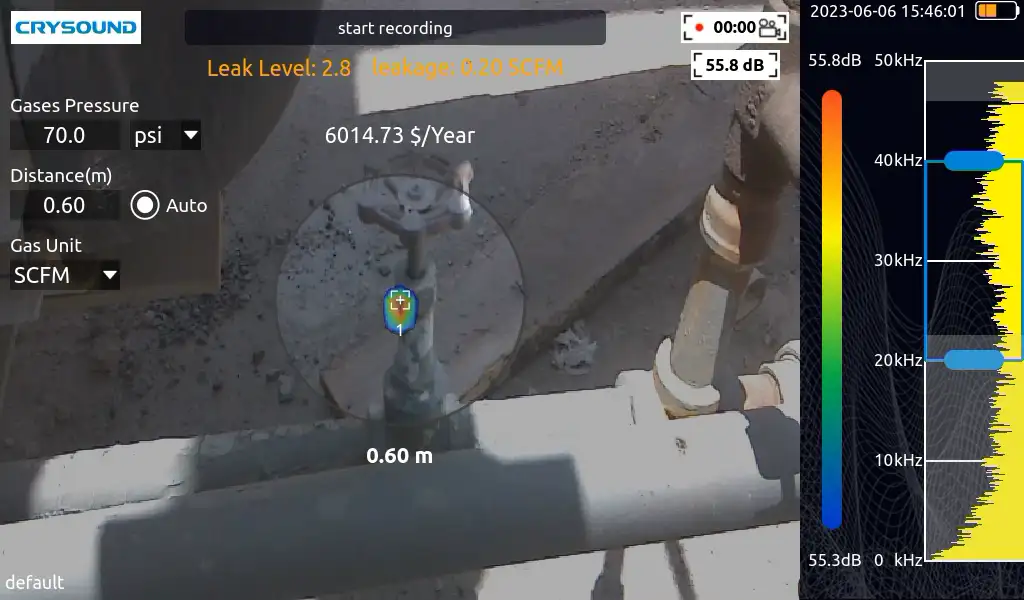
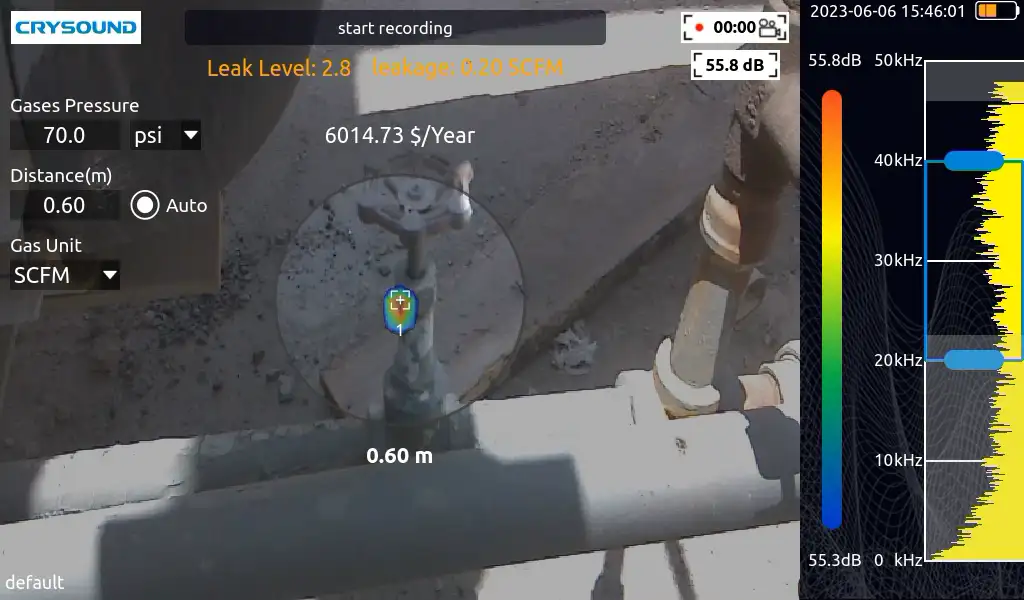
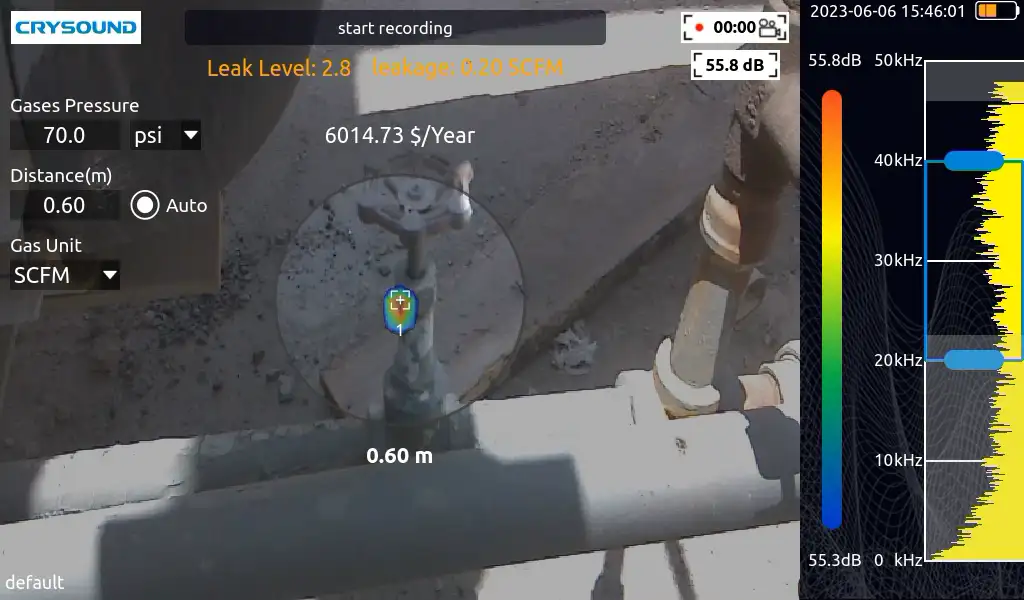
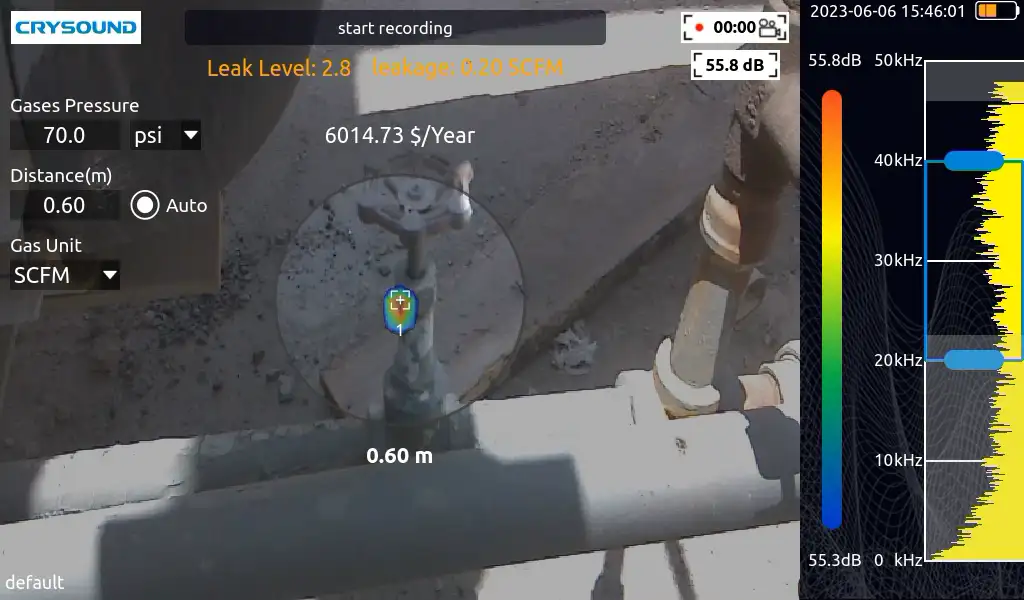
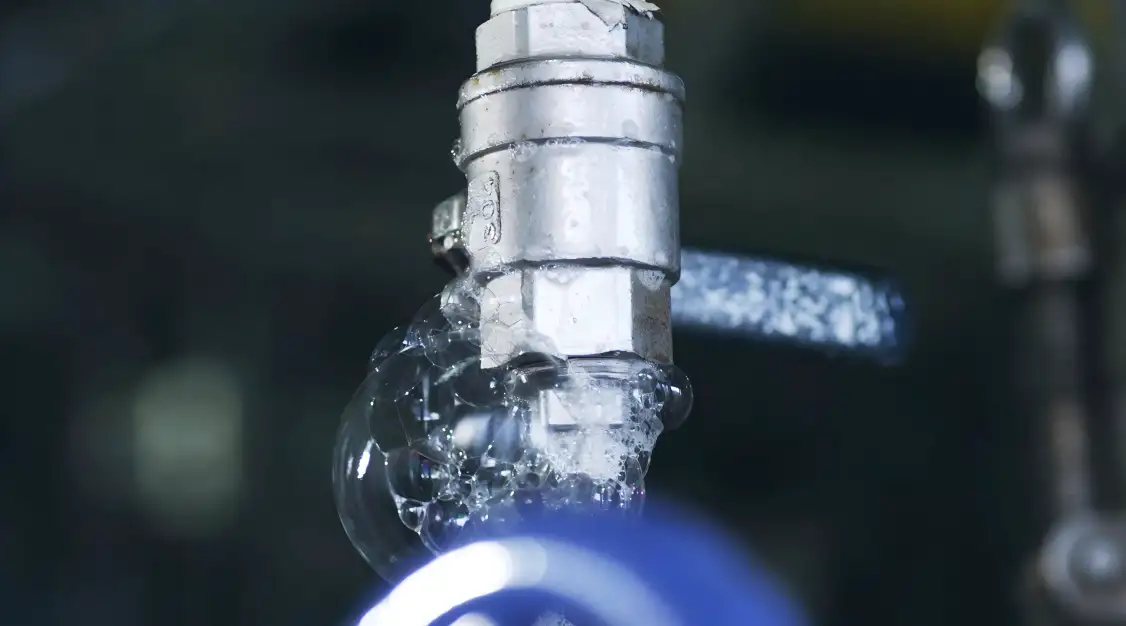
In the past, leak detection demanded substantial resources in terms of manpower, materials, and time, leading to high operational costs. For instance, using soapy water to identify leaks in a chemical plant could take several weeks. Furthermore, for safety reasons, leak detection was often limited to production shutdown periods, adding to the overall complexity and expense.
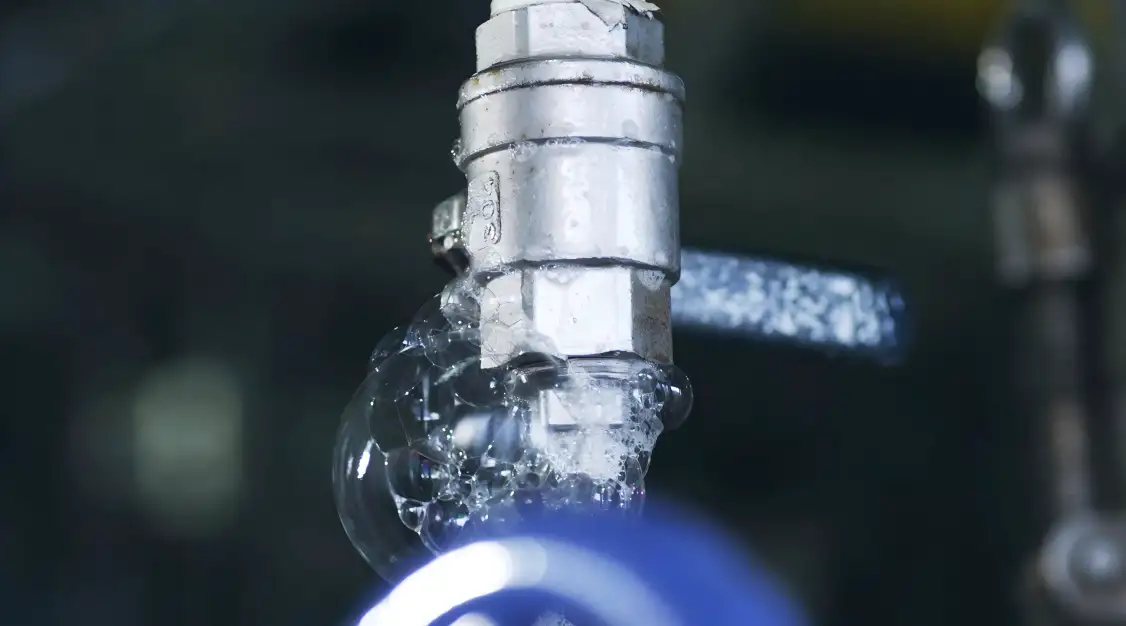

Unlike traditional leak detection methods like soapy water or gas concentration alarms, CRYSOUND utilizes advanced acoustic imaging technology to detect leaks. Our system identifies the distinct sound frequencies generated by gas leaks, enabling safe and efficient detection from a distance, regardless of the gas type.

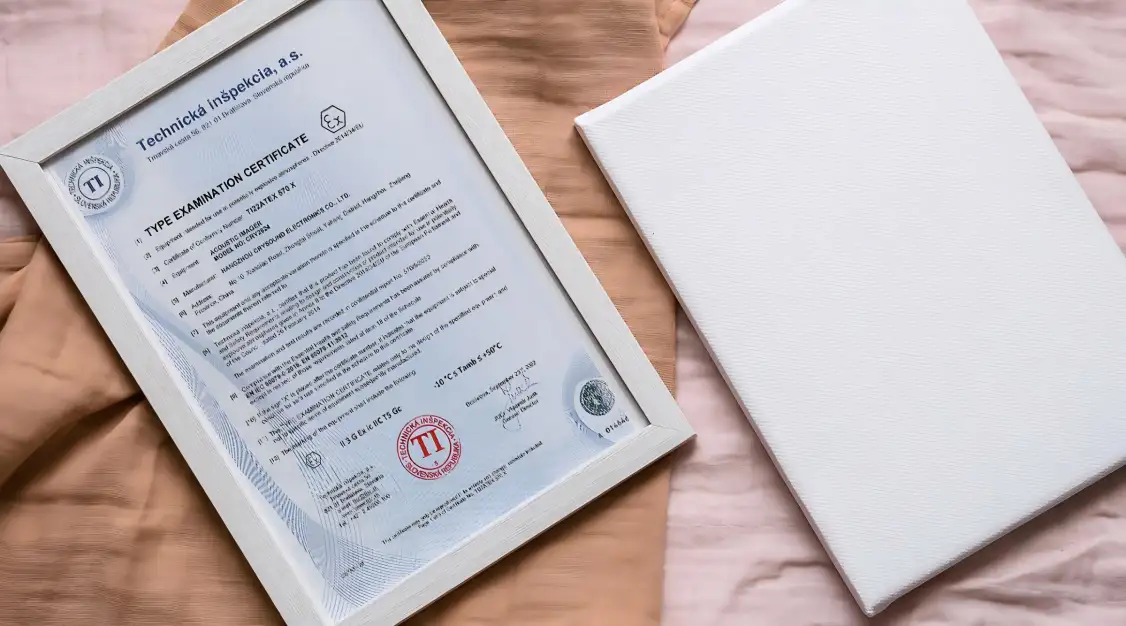
The ATEX-certified CRYSOUND acoustic imaging camera has demonstrated exceptional effectiveness in detecting hazardous gases like hydrogen and acetylene, ensuring the safety and reliability of equipment in the field.
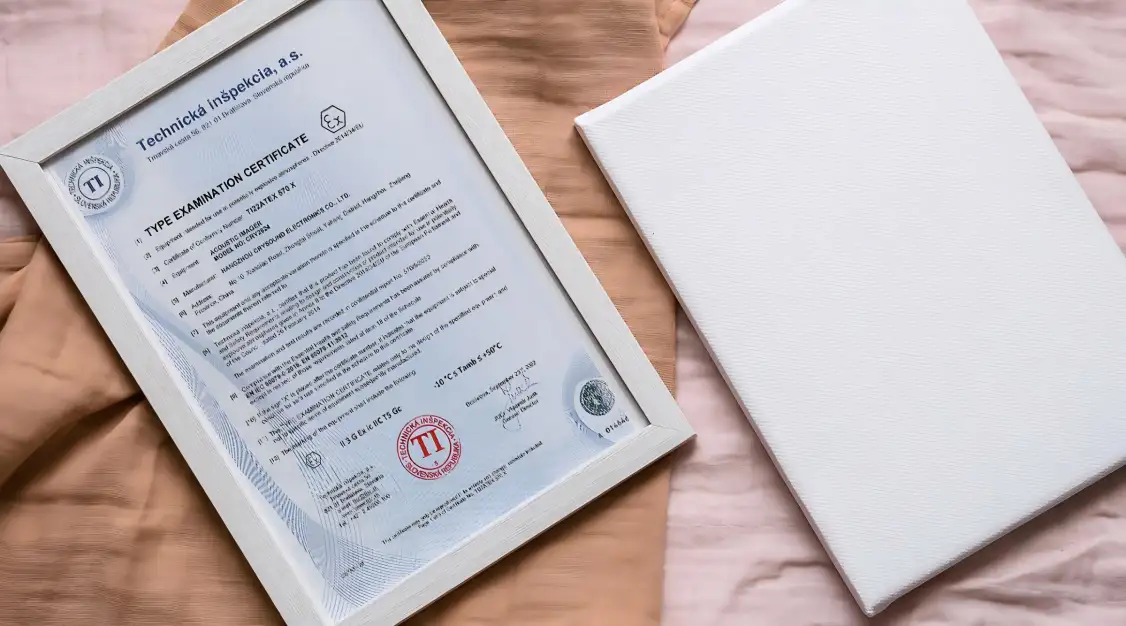
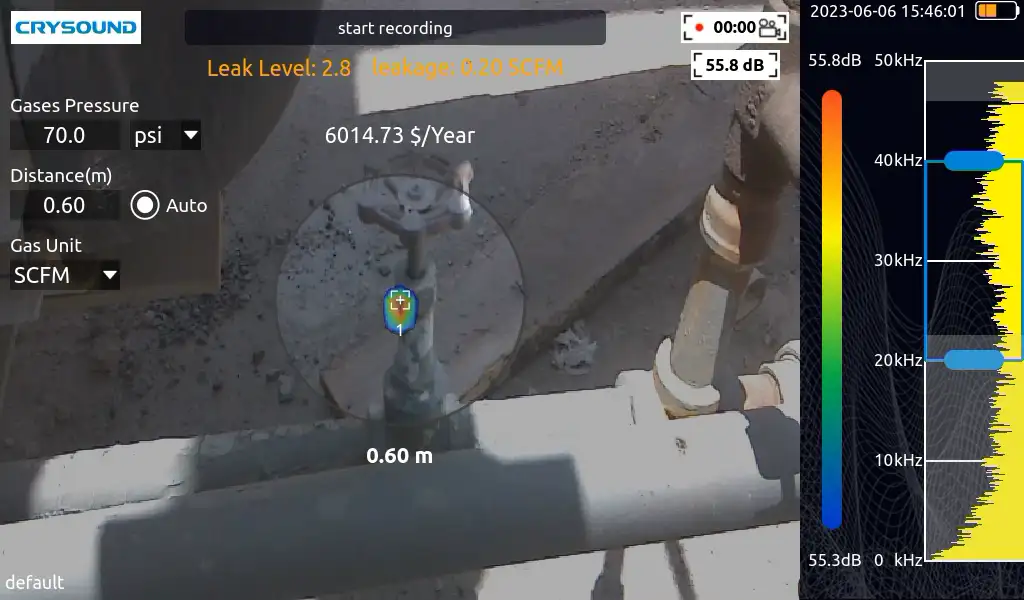
Chemical plants benefit greatly from acoustic imaging technology, which reduces the need for extensive materials, manpower, and time, ultimately driving down overall costs. This technology simplifies the detection of even small leaks of toxic or explosive gases, making it easier to align safety protocols with reliability objectives.
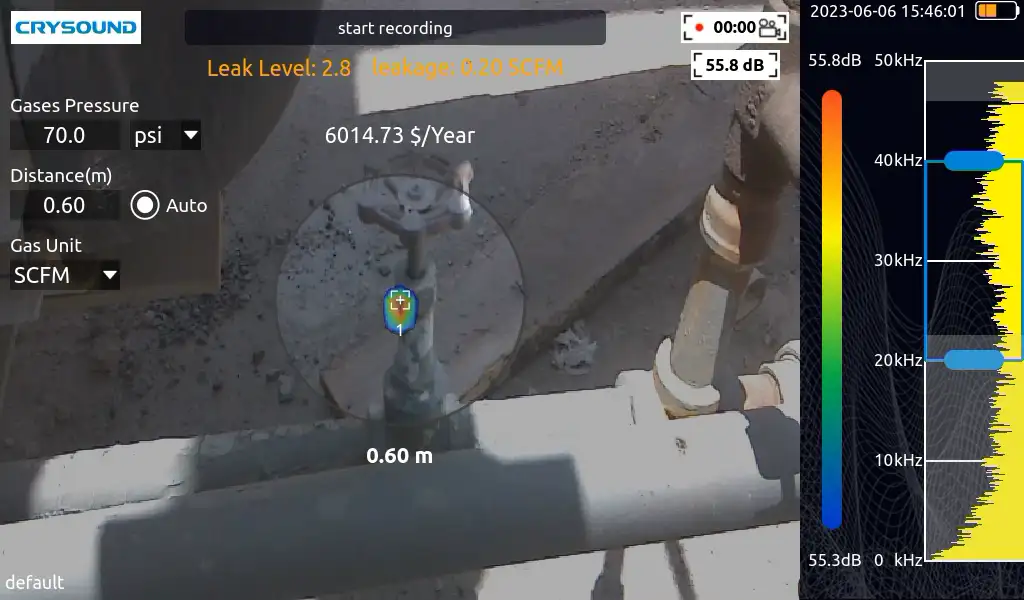
System Devices
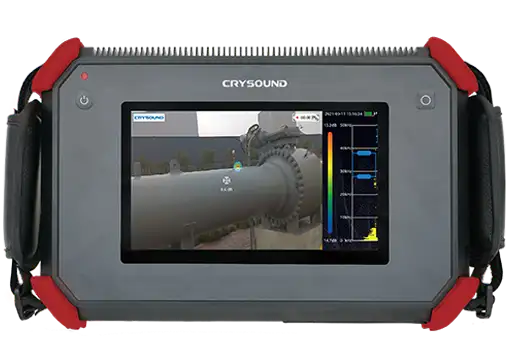
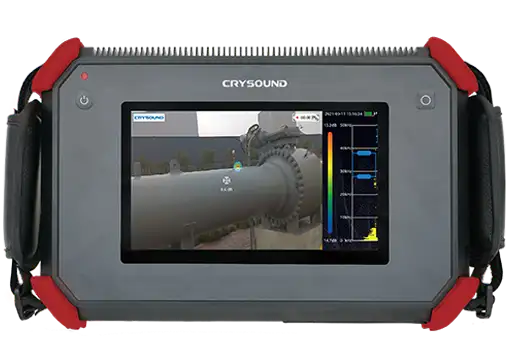
The CRY2624 is a 128-mic industrial acoustic imaging camera and is designed for use in explosive environments within the chemical and energy industries. Featuring a robust aluminum alloy shell, this device is built to withstand complex and dynamic work conditions. It offers real-time sound image display, significantly improving the speed of detecting pressurized or vacuum leaks compared to other methods.
The CRY2624 is ATEX certified with a rating of II 3G Ex ic IIC T5 Gc, ensuring safe operation in potentially explosive atmospheres while adhering to stringent safety standards. The device supports camera and video modes, providing flexible on-site data recording. With an expandable large-capacity TF storage card, test results can be quickly exported and reported. This camera helps industrial facilities minimize losses from gas leaks, partial discharge, and other accidents, enhancing overall safety and operational efficiency.
.png)
